Sinico Service: an insight into advanced manufacturing and innovation
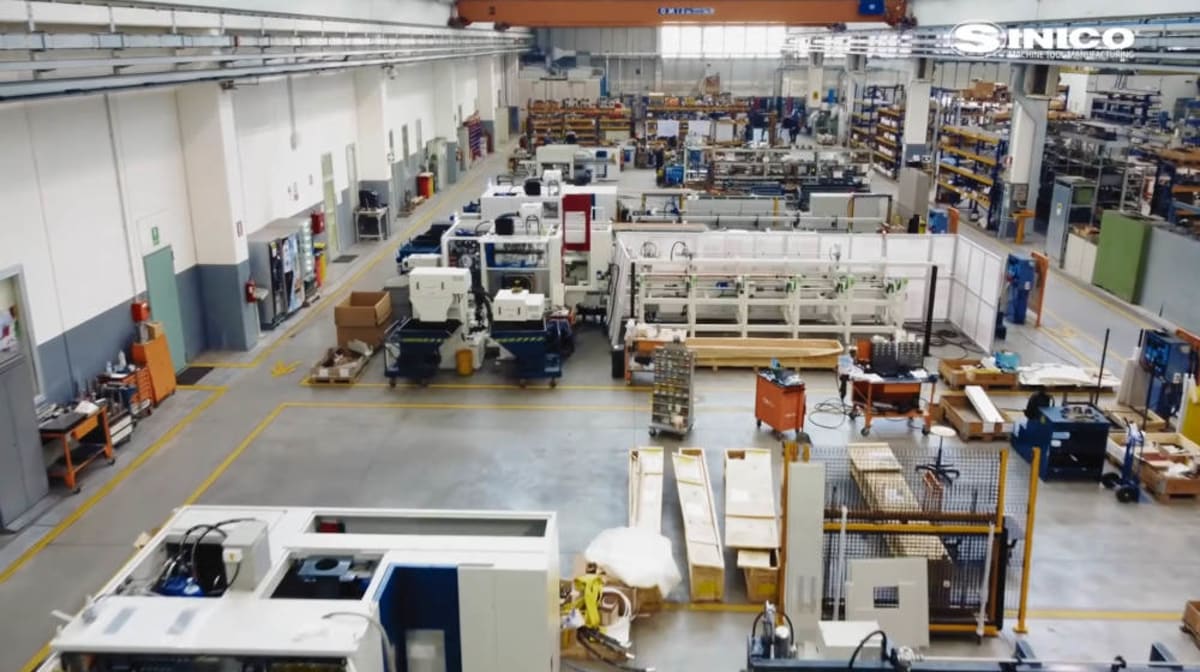
In its latest Factory Video, Sinico Service, a company specializing in the design and production of automatic transfer cutting and end processing machines, takes us on a virtual tour to explore its state-of-the-art departments and production processes.
A cutting-edge production facility
Sinico Service headquarters is a highly technological hub designed to optimize operations and guarantee the highest levels of precision. From cutting and storage to quality control, the company’s facilities are equipped with the latest technologies, enabling seamless execution of complex production processes.
Key production areas and processes
1. Cutting and storage: the first step in Sinico's production process is cutting, where materials are precisely cut to meet the required dimensions. This stage is closely integrated with the storage area, ensuring efficient raw materials management and quick access to components for subsequent production phases.
2. Heat treatments: a critical process for enhancing material durability and performance, heat treatments ensure components undergo controlled heating and cooling to achieve optimal hardness and structural properties for their intended application.
3. Roughing and milling: the roughing and milling processes are essential for shaping and refining raw materials into the required components. Using CNC machines, the company assures high precision and repeatability, delivering parts with tight tolerances.
4. Laser marking: laser marking is used to apply precise and durable markings on components. Whether for part identification, traceability, or brand recognition, Sinico's laser systems deliver high-quality results without compromising material integrity.
5. Turning and grinding: turning and grinding are crucial processes for achieving the components final shape and finish, ensuring they meet the required specifications with precision.
6. Metal fabrication: although not commonly found in many production facilities, Sinico's metal fabrication department adds a versatile dimension to its manufacturing capabilities, supporting the construction and assembly of exclusive Sinico products, such as standard and customized loaders.
7. Painting area: in this area, components receive their final finish, ensuring both aesthetic appeal and protection against external factors. Whether for corrosion resistance or a polished appearance, the painting process is critical for providing product longevity.
8. Vertical storage system: designed to optimize space and efficiently organize parts, this system allows for better inventory management, quick retrieval, and a streamlined workflow throughout the entire production process.
9. Quality control: the quality control department is equipped with the most advanced tools and technologies to perform thorough inspections at every stage of the production process. This ensures that all products meet the company's high standards and customer specifications.
10. Testing processes: Sinico conducts rigorous testing in the presence of the client to confirm that every final product and component complies with the required performance standards.
For more information about Sinico Service products, please contact the company using the details provided on this page.
