A state-of-the-art galvanic hub for Bulten Group in Poland by OMIG
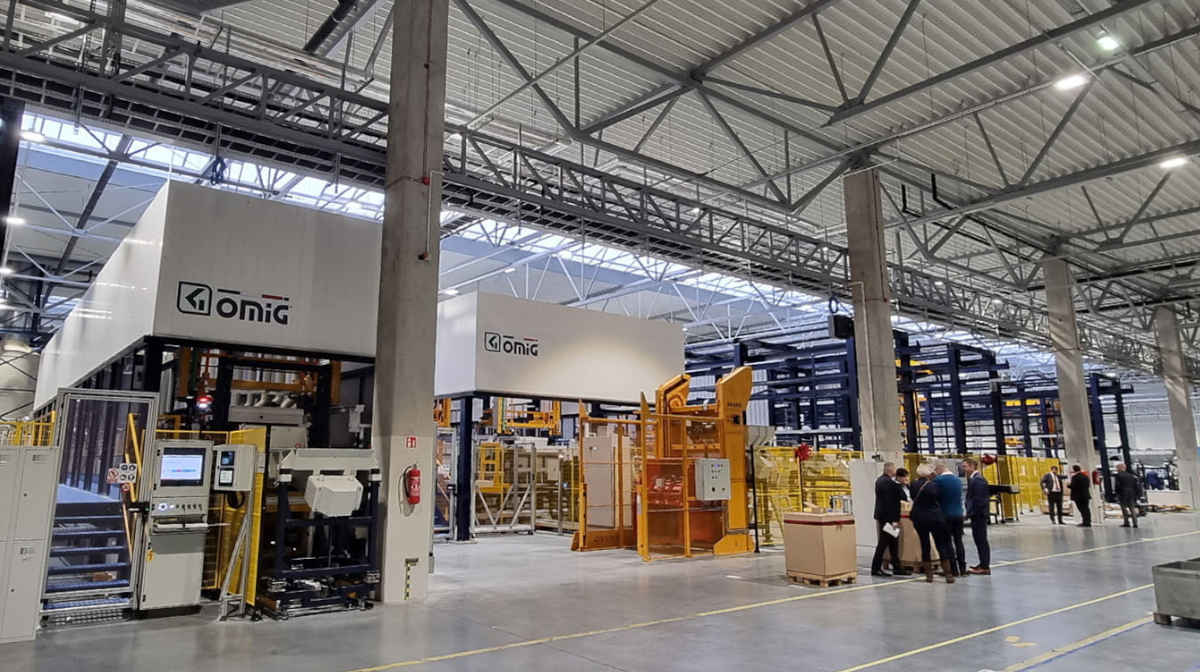
In recent years, many large industrial groups have opted to internalize their galvanic processes. This complex strategy requires advanced systems, technical know-how, and a reliable partner.
OMIG Srl, an Italy-based company with internationally recognized expertise in the design and construction of galvanic systems, has established itself as a technology partner for major projects. A concrete example is the collaboration with Bulten Group, one of the leading global fastener manufacturers for the automotive sector.
The galvanic systems in detail
At Bulten Group’s production site in Wieprz (Poland), OMIG designed and installed a complete line of high-performance galvanic systems. These systems are engineered to ensure continuous productivity and consistent quality in surface treatments for automotive fasteners and are adaptable to all types of screws requiring corrosion protection.
1- Phosphating system with barrel and basket finishing (400 kg/h)
This system is dedicated to preliminary treatment via phosphating, followed by basket finishing. The combination of barrel and basket optimizes the process for parts with varying sizes and geometries, improving coating uniformity and batch handling.
2- Zinc and zinc-iron (Zn and ZnFe) plating system with barrel and basket finishing (1,200 kg/h)
This high-capacity line is designed for continuous processing of large volumes. The barrel ensures uniform coverage even on complex parts, while basket finishing allows quick drying and efficient output handling.
3- Zinc-nickel (ZnNi) plating system with barrel and basket finishing (1,000 kg/h)
The zinc-nickel system, increasingly requested in the automotive sector due to its high corrosion resistance, is designed to combine quality output with sustainability, optimizing water and reagent consumption.
4- Fully automatic and interconnected dehydrogenation system
A strategic element of the process, this system removes residual hydrogen after galvanic treatment, critical to preventing hydrogen embrittlement in treated materials. Fully integrated with the plating lines, it is programmed to initiate cycles within 2 hours after electroplating. Cycle durations can be customized from 2 to 12 hours, depending on batch specifications and the mechanical requirements of the end customer.
All systems are managed via a centralized monitoring and control system, allowing full traceability of batches, real-time monitoring of process parameters, and optimization of preventive maintenance.
Looking for a partner to guide your galvanic internalization process?
You can count on OMIG’s experts, available through the provided contact information.