‘Manufacturers of precision steel tubes often feel left alone with automotive specifications’
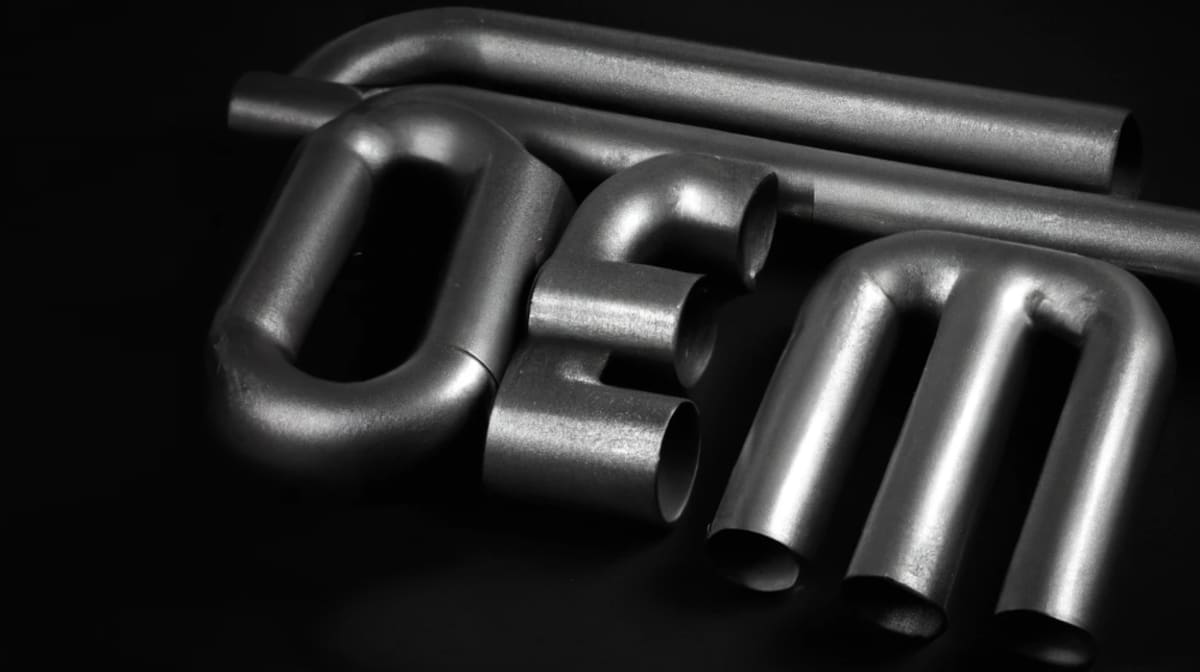
The article delves into the challenges faced by manufacturers of precision steel tubes, particularly in response to evolving demands from the automotive industry. These tube makers encountered a pivotal shift towards high-strength steel in the late 1990s, prompting a surge in demand for precision tubes capable of withstanding rigorous automotive applications. As various high-strength steel variants emerged, manufacturers grappled with technical complexities and operational hurdles, compounded by limited technical discussions within the industry. Amidst these challenges, the article highlights the author's expertise in consulting on high-strength steel high-frequency welding, offering insights into strategic approaches and technical considerations. Juergen Stindt brings over three decades of experience in tube manufacturing, offering practical solutions and personalized consultations.
Behind the seams: insights into high-frequency welding
They were successful on the market for many years - the manufacturers of precision steel tubes; some were founded in the post-WWII reconstruction period and supplied precision steel tubes to all possible industries, including the automotive industry.
Shift to high-strength steel
In the late 1990s, automotive Original Equipment Manufacturers (OEMs) began seeking alternatives to solid materials, such as using tubes instead of solid components - for example for stabilizers - as a means of conserving resources. The primary objective was to reduce vehicle weight during construction. This shift required materials to endure the stresses of a vehicle's lifespan with less bulk, leading to a significant surge in demand for precision steel tubes crafted from high-strength steel.
The emergence of high-strength steel variants
Boron-manganese steels, like grades 22/26/34MnB5, were initially prominent. These steels had a high carbon content and various alloy components that differed significantly from batch to batch.
Additionally, dual-phase steels like DP 600/800/1200 emerged, characterized by high purity levels and strength derived not solely from carbon content but from other alloy components, mirroring the approach of high-strength structural steels such as S490 (which utilized manganese, aluminum, nitrogen, among others). These materials were in high demand by OEMs and their suppliers. It was about stabilizers, steering parts, vehicle seat tubes, vehicle door beams, and others. Initially, German and then European steel tube manufacturers were sought after to fulfill these requests.
Challenges for steel tube manufacturers
Established steel tube manufacturers had overhead costs, which allowed them to employ engineers who oversaw production. Despite the challenges of high-frequency welding due to the high carbon content and high springback during forming and hardening of the material on the tube welding line, the engineers and experienced machine operators were able to produce tubes that met the high-strength specifications.
Mainly for price reasons, these specifications were also requested outside of Europe. The smaller manufacturers didn't have any overheads and if they were looking for engineers to meet the high demands of HF-welding, for example, they couldn't be found on the job market. Nevertheless, they did not want to miss this opportunity to supply European vehicle manufacturers. Large steel tube manufacturers also had a hard time; although there was enough staff available, there was no free capacity to run tests on the tube welding lines to meet the requirements of the new steel grades. For a long time, no particular attention was paid to the technical possibilities for producing precision steel tubes. The HF-welding of tubes has forgiven many mistakes with conventional steels, so the tube welding machine operators were often left alone with their problems, but somehow it worked and the output of the tube welding line was quite satisfactory.
Due to very different interests, there have not been any intensive technical discussions about the production of high-strength precision steel tubes among the tube welding machine manufacturers, the suppliers of welding generators, and the tube manufacturers.
Consulting on high-strength steel HF welding
All these situations and circumstances allowed me to start consulting on HF welding of high-strength steels for steel tube production - I was asked to help. This path, which I took a good two years ago, has been easy to follow so far. Orders have been coming in slowly but steadily because many manufacturers had and still have problems with HF welding of special grades. There was a need to respond to the customer's respective requirements and circumstances and to achieve a good result together. Every welding line is different, every welding line operating crew has a different philosophy for setting up the line, different suppliers have welding generators with different capacities, and different manufacturers were involved for example for the internal scarfing of the tubes, there are different raw material qualities and much more. As different as the tube manufacturers are, their goals are the same: to become a new reliable supplier of high-strength precision steel tubes, or to expand the position already achieved without major investments.
A small success story emerged, word of my activities spread quickly, and no one hires a consultant who doesn't have good references.
Tube welding line manufacturers also sought my advice. As a common practice, after the delivery and acceptance of a new welding line, they are restricted from daily tube welding practices. Consequently, they face challenges in expanding their expertise, particularly in HF-welding certain difficult tube dimensions.
Other tube welding line manufacturers encounter pressure from customers to the extent that they withhold remaining payments for a new welding line until they acquire new knowledge about welding special steels.
In the picture: a successfully tested sample of an expansion test on a tube, highlighting that the weak point wasn't the weld itself.
And finally, the most important players, the manufacturers of precision steel tubes, are taking on the challenge themselves. For example, they are capitalizing on a temporary lull in the tube market to conduct intensive tests, focusing on welding high-strength tubes. They seek support without reservations and demonstrate openness in dealing with and discussing their problems.
In most cases, there wasn't much left to improve the welding parameters to ensure the long-term durability of the weld seams, but many small problems add up to a big one.
A misunderstood parameter
I appreciate the technical writing of Dr. Paul F. Scott's The Effects of Frequency in High Frequency Welding from April 16, 1996. He describes the welding parameter frequency in a special way, “One of the most important parameters in high-frequency tube and tube welding is the welding frequency. Yet, until recently, it has been one of the most misunderstood!” However, the text does not tackle the challenge of welding high-strength steels, as it was published before the emergence of OEM requirements regarding this matter. Scott also lists detailed mathematical ways to determine the individual parameters, which I studied intensively but found unsuitable for practical application. However, despite its limitations, I still support the central thesis mentioned above.
A frequency predicament
Tube manufacturers usually fail to reliably produce long-lasting weld seams from high-strength steels because the frequency range of the welding generator does not provide the required window or the existing frequency range cannot be permanently reduced. Inquiries made to the generator supplier regarding the material and specific tube dimensions frequently yielded questionable responses. For example, other tube manufacturers were mentioned without being named who still manage to weld extremely thick-walled tubes at high frequency. The answers do not stop at personal defamation, either. “Your method of HF-welding is old-style. Find out about more modern methods!” However, personal on-site assistance is rarely offered. If provided, it often proves insufficient, as I experienced firsthand with a Chinese tube manufacturer. Despite requests, tube samples with well-welded durable seams from 'modern' tube manufacturers are unavailable. It is reasonable to assume that large welding generator manufacturers prioritize advising on products readily available in their portfolio, focusing on items in large quantities that need to be sold.
Strategies and considerations in precision steel tube welding
Despite initial criticism, I chose to weld the precision steel tubes at a lower frequency as a strategy. So far, I have successfully assisted eight customers worldwide using this method. The other welding parameters must, of course, be adjusted accordingly, following established practices. Steels with high carbon content (≥ 0.3%) require different treatment on the welding line compared to those with low carbon content.
Additionally, there are other high-strength steels with low carbon content, such as DP steels, which derive their strength from various alloys, necessitating different welding settings. Cooling plays an essential role; existing cooling lines must be converted and adapted. Even the welding speed should not be underestimated as a parameter for success. While there are other techniques available, albeit limited, for reducing the frequency output from a welding generator that is too high.
Questions also arise, for example:
◎ How is the structure of the impeder and its position relative to the inductor?
◎ Is the cooling capacity for the impeder sufficient when the load on it is increased?
◎ Furthermore, how durable are the tools used for all welding settings, and are they suitable for continuous operation in this case?
Some tube manufacturers have contacted the manufacturer of the internal scarfing system, expressing complaints that they claim render the system unusable. In most cases, the response to this issue is that the material must be made scarfable by selecting the right welding parameters. This entails choosing welding parameters, including cooling, that allow the material to be machined, ensuring the possibility of good internal and external scarfing. No scarfing ring or external scarfing tool can permanently scarf steel strengths greater than Rm ≥ 1700 MPa in good shape and appearance. Permanent undercut is not possible at all with this strength.
◎ How are the tube samples assessed after the destructive tests?
◎ How are micrographs assessed correctly and following the requirements?
I am well-equipped to address these questions and more, provide training for your management and operating team, and customize your welding line to meet your customer’s specifications. For instance, I am available for an initial meeting at the Tube 2024 trade fair in Düsseldorf, Germany from April 15th - 19th. Contact me via cell phone at +49 1709 215 473.
About the author:
Juergen Stindt, 62 years old, Mechanical Engineer with an MBA, boasting over 30 years of hands-on experience in tube manufacturing across various management roles including:
- Vincenz Wiederholt, Q-Manager
- PTC Alliance, Unit Manager
- Jansen, Plant Manager
- Prinz-Mayweg, Technical Manager
- Mubea, Project Manager for new factories, in collaboration with temporary factory management
Current client base includes India, China, Japan, Turkey, Spain, Italy, and Germany.
--
You might be interested in reading:
Tube Düsseldorf exhibitors' list: the Expometals.net Hall of Fame
"Witnessing machines in action, that's the essence of wire & Tube 2024"